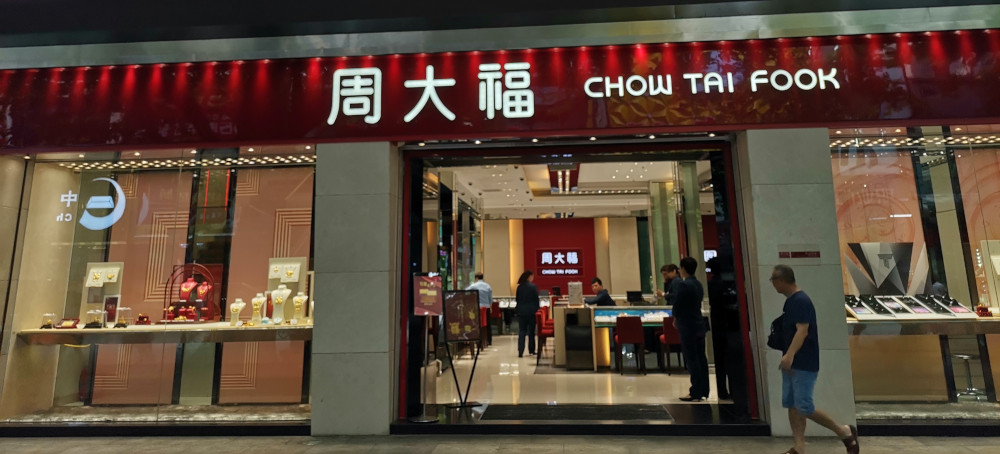
Business Needs:
- To optimize supply chains from production to retailing in order to minimize cost and maximize the yields according to the operational constraints and resource availability.
- To make decisions for factories loading, supplier selection, order allocation, customer order scheduling, material supply scheduling etc.
- To optimize delivery packing, scheduling and routing, to achieve the business goal with the lowest costs.
- To improve the automation level of existing product management operations in retailing (including purchasing, allocation and rebalancing); to improve working efficiency and accuracy.
- To establish predictive models for better stock efficiency and maximize sales opportunities.
- To track the effectiveness of the on-going product management strategies.
Challenges:
The challenge in retail chain is that the majority of the products have low sales quantities with similar styles, which make normal statistical model of safety stock not work properly and require a new model to mimic the customer buying behavior for better sales prediction. The challenge in manufacturing requires to optimize the overall cost from the lots of variables in factories loading, supplier selection, order allocation, customer order scheduling, and material supply scheduling.
Solutions:
Based on past 10 years of sales history, generate a new model that can give a good prediction on sales for both fast moving and slowing moving products, by analyzing the product similarities with the knowledge on how a customer choose a product to buy. The overall cost in manufacturing is optimized by building a model using constrain programming and mathematical programming.